Years ago, I made a post on this subject but of course the pictures are now gone thanks to Photobuckets' decision. Recently, customers have sent me a number of scales to rebuild so I have gotten back into this part of restoration. Members have requested further information, so here goes. This post will be far more comprehensive than the first one.
There are 2 basic types of officer chin scales and I am going to limit this post to them. There are of course OR's versions of these but I am not going to get into that. The M95 OR's have a special end fitting which hooks over the M91 posts and repairing those is way beyond my expertise. Back to the officer scales....2 types...flat scales for infantry and convex (curved) for mounted troops. If you encounter scales which are not obviously of either type, check out the chin scale boss which holds the scale to the shell. The convex boss will always be curved and the flat scale boss will always be flat
A pair of original neusilber convex scales and bosses. For our newer members, the fittings on any helmet matched the buttons on the regimental tunic. Some regiments for example, Pioneers had silver buttons and thus, their Pickelhauben have neusilber (nickel plated) fittings on them.
The reverse side of the neusilber scales. When worn on the helmet, the scales link together and on this original pair we see a round "button" on the male side and a "keyhole" opening on the female side. There is another male/female configuration which involves a "T" shaped male fitting and a simple slot on the female side. Note also the thin leather strap and buckle. The scales were intended to extend down the cheeks and supposedly protect that area. This goes back to ancient times. The thin strap was cinched up around the chin to secure the helmet to the head when supposedly going into battle.
Civilization occurred with the cultivation of grain, and then we see the development of helmets to protect the head and face of warriors. So if you choose to investigate these on the internet you can see what I am talking about. All for now.
A picture of the 2 types of bosses....flat infantry on the left and convex cavalry on the right. The size of these varies with the size of the large first scale. The circular design and centre button can also be different from helmet to helmet.
A pic of flat infantry scales rebuilt for me by the late George B. I sent him some bits and pieces and he had some parts and came up with these. Typically, the end fitting and the first 2-3 scales break off over time and are missing. In this case, the key hole end fitting is not strictly correct for this T fitting but it will work. Note as well the 2 end staples in the largest scale are always vertical, the rest of the scale are horizontal. When you take a scale apart, you start with the largest end scale and work back to the end fitting. The reverse is true when rebuilding a scale.
There are 2 basic types of officer chin scales and I am going to limit this post to them. There are of course OR's versions of these but I am not going to get into that. The M95 OR's have a special end fitting which hooks over the M91 posts and repairing those is way beyond my expertise. Back to the officer scales....2 types...flat scales for infantry and convex (curved) for mounted troops. If you encounter scales which are not obviously of either type, check out the chin scale boss which holds the scale to the shell. The convex boss will always be curved and the flat scale boss will always be flat
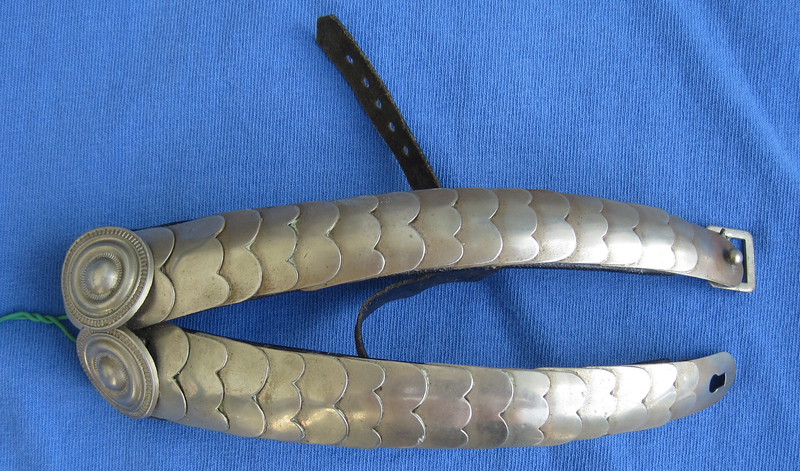
A pair of original neusilber convex scales and bosses. For our newer members, the fittings on any helmet matched the buttons on the regimental tunic. Some regiments for example, Pioneers had silver buttons and thus, their Pickelhauben have neusilber (nickel plated) fittings on them.
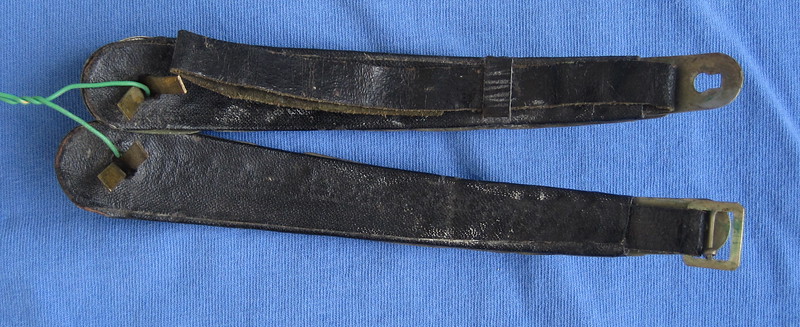
The reverse side of the neusilber scales. When worn on the helmet, the scales link together and on this original pair we see a round "button" on the male side and a "keyhole" opening on the female side. There is another male/female configuration which involves a "T" shaped male fitting and a simple slot on the female side. Note also the thin leather strap and buckle. The scales were intended to extend down the cheeks and supposedly protect that area. This goes back to ancient times. The thin strap was cinched up around the chin to secure the helmet to the head when supposedly going into battle.
Civilization occurred with the cultivation of grain, and then we see the development of helmets to protect the head and face of warriors. So if you choose to investigate these on the internet you can see what I am talking about. All for now.
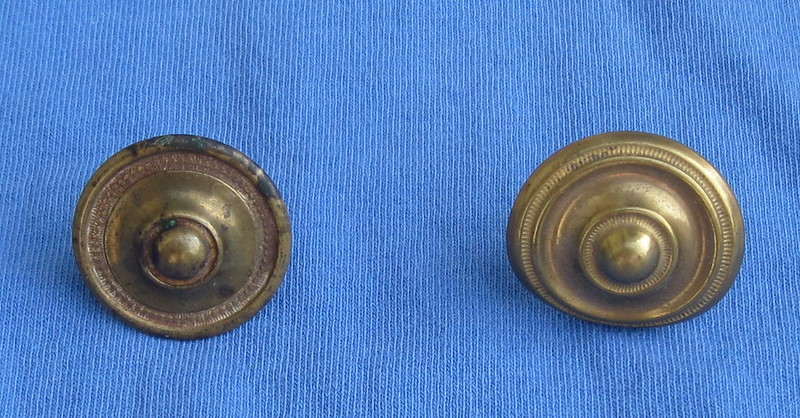
A picture of the 2 types of bosses....flat infantry on the left and convex cavalry on the right. The size of these varies with the size of the large first scale. The circular design and centre button can also be different from helmet to helmet.
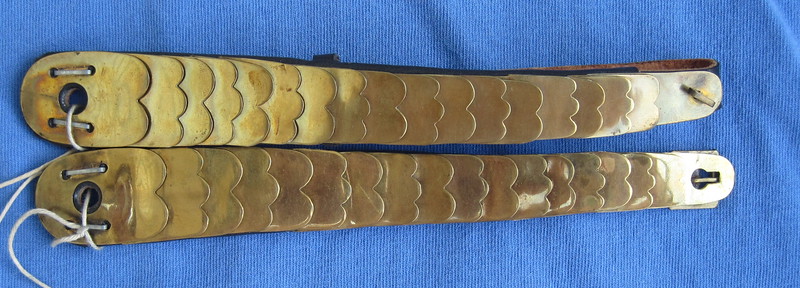
A pic of flat infantry scales rebuilt for me by the late George B. I sent him some bits and pieces and he had some parts and came up with these. Typically, the end fitting and the first 2-3 scales break off over time and are missing. In this case, the key hole end fitting is not strictly correct for this T fitting but it will work. Note as well the 2 end staples in the largest scale are always vertical, the rest of the scale are horizontal. When you take a scale apart, you start with the largest end scale and work back to the end fitting. The reverse is true when rebuilding a scale.